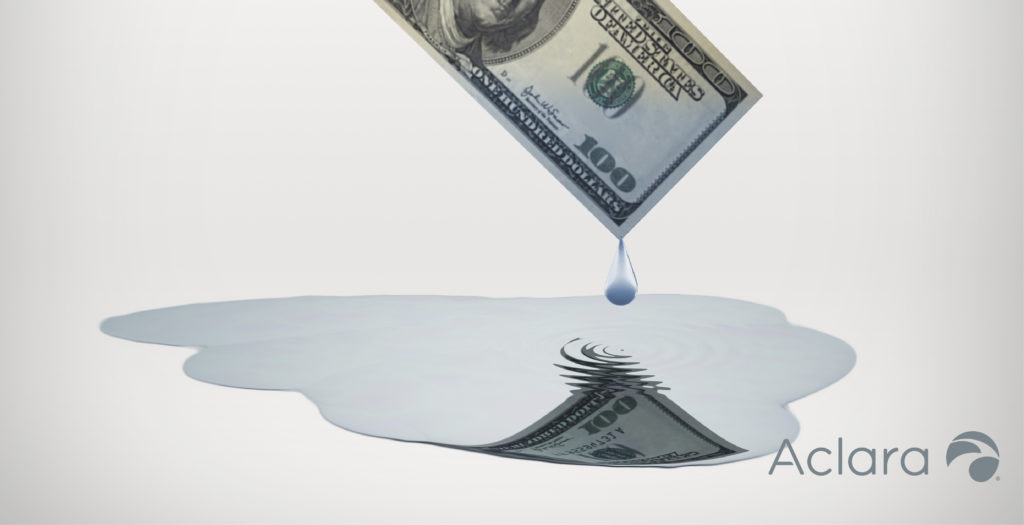
Utilities that choose not to install proactive leak detection know exactly how much they are ‘saving’ by avoiding that investment. Unfortunately, they often have no idea of how much they are actually ’paying’ to forego it, since 65 to 75 percent of water leaks never surface to prove their hidden expense. Now, with challenges related to water scarcity, regulatory reporting demands, advanced metering infrastructure (AMI) implementation, and an increase in aging infrastructure, it’s a better time than ever to reevaluate those costs.
Where’s the motivation to identify water leaks?
One motivation behind utility operators becoming more sensitive to leak detection and repair is the advent of mandatory water loss reporting in states such as California, where years of drought have increased pressure on precious source water supplies.
Maximize the value of water AMI. Download the white paper.
Another emerging motivation is the realization that most leaks never surface. Contrary to those who claim, “the leaks find us,” the reality is that water finds its own path of least resistance and only one leak out of three ever sees the light of day. Even when water leaks do surface, some long after they have started, they might do so hundreds of feet from the original source. This can extend the time required to locate and repair the problem or multiply the cost and complexity of excavation and repair.
Documented events such as a substantial leak that found an underground escape path into a storm drain unnoticed and an assumed ‘stream’ that ran out of a wooded area along the back of a housing development for more than 32 years are just two examples of how major water losses can go undetected for extended periods.
Calculating the costs of leaks vs. leak avoidance
Not knowing exactly how much water is escaping from how many leaks in how many undocumented locations makes it hard to calculate the costs of treated water loss. The ideal first step toward determining realistic numbers for recoverable water losses and the payback potential of leak detection technology is conducting a water audit using the AWWA’s Free Water Audit Software.
Identifying leaks that are cost-effective to repair will not generate new revenue but will lower operating costs for chemicals, electricity, and the raw cost of lost water, and leave more of an operating budget to achieve other tasks or stave off dreaded rate increases.
Even without a full-fledged audit, it is still possible to glean hints of how much the lack of good leak detection is costing a utility. Look to identify the cumulative percentage of known and unknown annual water losses — typically double-digit losses — and the exceptional maintenance costs recorded over the course of the year.
Identifiable water losses. Distribution systems monitored by district metered areas make it practical to estimate how much water is being lost in certain zones. Once a definite leak is discovered, it is also easier to track escalating losses, especially if hard-to-locate or inoperable valves delay leak repairs.
Indirect costs associated with leak events. Aside from basic physical repair costs, other avoidable costs associated with smaller leaks growing into larger problems can be tracked by annual analysis.
- Premium rates paid for emergency repair part rush orders and expedited shipping costs are two often overlooked costs that should be tracked on an annual basis.
- Increased repair complexity for leaks that escalate in severity, potentially becoming sinkholes before being discovered, typically incurs elevated component and labor costs. In extreme cases, that can include heavy equipment rental, more extensive traffic control, and perhaps penalties for disrupting major traffic routes or critical infrastructure such as hospitals or schools.
- Payments for damages to private property as a result of water main breaks are another potential out-of-pocket cost. Insurance might cover certain amounts, but self-insurance and higher premiums for repeat occurrences can eventually exceed the cost of a leak detection investment.
The added value of AMI
While manually conducted leak surveys using conventional listening devices, noise loggers, or even cellular communication solutions are cost-effective, using leak detection equipment in conjunction with AMI can accelerate the payback period for multiple reasons.
- Labor. Integrating acoustic leak detection equipment as part of AMI infrastructure continually feeds data on new and progressing leaks to key operations personnel automatically, without conventional costs for manual labor to shift equipment or collect readings zone by zone.
- Continuity. Automatic leak monitoring and reporting creates a new leak survey every day without human intervention. AMI makes it easy to find and monitor leaks, which in turn can help utilities determine when they pass the economic level of leakage, where the cost of water loss exceeds the cost of repair.
- Automated reporting. Establishing automated reporting through an AMI system also supports objective data creation independent of user skills or other human involvement.
- Cost avoidance. Any leak detection effort will find the low-hanging fruit of the most obvious water leaks in the early phases of implementation. By making leak detection part of a continuous AMI monitoring program, water distribution utilities can become more proactive at water-loss avoidance.
This white paper on Using Advanced Metering Infrastructure With Analytics To Reduce Apparent And Real Water Loss outlines the overall process for water loss control of apparent losses and real losses, intervention strategies, analytics, and acoustic leak detection.
Reaping the positive payback of ‘knowing’
Every utility’s payback period varies depending on the age, size, and circumstances of their distribution system. Knowing the total volume of water treated/pumped per day, the cost per million gallons to treat that water, and the percentage of recoverable loss identified from the water audit, however, enables the calculation of actual dollars wasted per day. Conservatively calculating the savings for recovering one-half to two-thirds of known water losses will enable them to project how quickly an investment in leak detection can pay for itself.
This free demo of analytical tools that deliver deeper appreciation of non-revenue water losses can provide better insights into maximizing water delivery and prioritizing work orders to recover those losses.
Additional informative resources on water loss audits include this AWWA white paper, these U.S. EPA water audit and water loss control guidelines, and the leak management section (pages 24-28) of this EPA best practices document.
This article first appeared on the Water Online website in May 2020